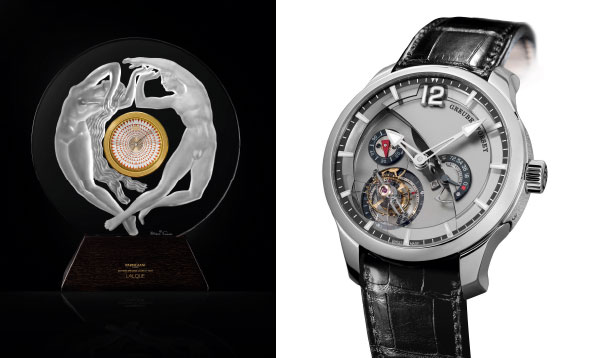
Les index de cette Greubel Forsey sont en nickel, déposés par croissance galvanique sur un anneau de saphir.
Derrière l’image luxueuse des montres, ces objets restent issus d’un processus de fabrication industriel. Même si de nombreuses étapes de ce parcours sont manuelles, elles passent de l’état de métal brut à celui d’objet fini par le biais de machines. Elles étampent, découpent, percent, affinent, forment et déforment la matière pour lui donner sa fonction. Le domaine n’a rien de glamour, mais il est fondamental car il conditionne le prix d’une montre, sa qualité et sa longévité. Autant dire qu’il s’agit du nerf de la guerre. Comme tous les domaines, il évolue vers plus de fiabilité, de rapidité et de productivité. Après avoir pris place dans les ateliers dans les années 1990 et 2000, les machines à commande numérique ont entrepris une seconde révolution, encore plus discrète que la première. Elles fabriquent sans contact avec la matière.
Scie micro-électrique
Les machines-outils, décolleteuses et étampes ont plusieurs limites. La première est leur brutalité. Lorsqu’un outil de coupe attaque la matière, il la déforme. Elle met du temps à revenir en place. Pour accélérer cette remise en place, certaines sont recuites, c’est-à-dire chauffées pour se relaxer. Puis elles subissent une rectification et l’on est sûr de leur forme. Ces longues opérations concernent principalement les boîtiers, pièces massives qui subissent de lourds traitements. Seconde limite, la taille des composants. Le développement de complications sophistiquées d’un côté et le besoin de fiabilité de l’autre font que les pièces les plus délicates ne sont pas taillées. Elles sont découpées à l’aide d’un fil à électro-érosion, un type de scie très fine qui utilise l’électricité en lieu et place de tranchant. Mais même lui a ses limites physiques. Pour produire des pièces alambiquées, l’horlogerie dispose de trois nouveaux outils.
Faisceau laser
Découper reste l’opération de fabrication la plus importante. Pour le faire sans contact, rien de mieux que le laser. Pour des pièces critiques et fines comme des ancres, des balanciers, des ressorts, il perce et détoure la matière sans la toucher ni la déformer. Mais les besoins d’usinage vont plus loin. Une fois la pièce produite, il faut encore affiner sa géométrie. Certaines roues d’ancre ont les dents d’un profil spécial, limées sur toutes les faces. Pour tailler un biseau d’un micron au bout de ces excroissances microscopiques et fragiles, le laser est l’unique option. Autre avantage, il est rapide et diminue les temps de fabrication.
L’échappement Strutec de Leroy utilise une découpe au laser pour affiner sa géométrie, et son efficacité.
La denture de ce disque en saphir transparent et rotatif est faite grâce au LIGA, qui permet à la Rotonde de Cartier l’Heure Mystérieuse d’exister.
Une ancre Laurent Ferrier : pour réaliser des formes à la découpe aussi fines et en volume, seul le silicium est envisageable.
L’échappement CHRONERGY de Rolex est réalisé en nickel grâce au LIGA.
Accumulation atomique
Parce qu’il faut parfois former au lieu de déformer, on peut accumuler de la matière au lieu de la retirer. La croissance galvanique fait s’amonceler des atomes de nickel sur une base, un substrat qui a la forme désirée. On façonne les pièces au niveau atomique et comme cette échelle est minuscule et lente, il s’agit de couches de l’ordre de 0,1 mm. Généralement, elles sont utilisées sur des pièces en saphir comme des cadrans pour y déposer des inscriptions ou des index.
Canon à ions
Le LIGA est un outil au nom barbare mais très précis et efficace. Issu des laboratoires de fabrication de micro-processeurs, il consiste à dessiner une forme sur une plaque de silicium pur. Puis un flux plasmatique (un jet d’atomes en quelque sorte) modifie la structure de la ligne dessinée et la supprime. La pièce est ainsi découpée comme une gravure profonde. Elle sort de ce processus propre, lisse, parfait. Cette technique permet de créer des empilements de formes complexes, de véritables volumes. C’est ainsi que sont façonnées toutes les pièces en silicium utilisées dans une montre, ancres, roues d’ancre, spiraux et ressorts. Pour profiter du silicium, il ne faut pas le toucher. Il est cassant et ne se travaille qu’avec la délicatesse d’un flux d’ions.